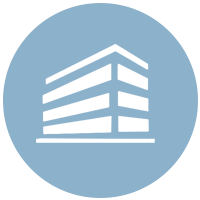
Wells Signature Products LLC (AKA: ACTON Materials Inc) Profile last edited on: 9/14/2010
CAGE: 3FL76
UEI: WJKEUKL6EWE4
Business Identifier: NO Business Identifier is currently available for this company. Is this YOUR Company?
Ensure accuracy and completeness of YOUR Company Profile by completing the brief Survey Instrument attached
Do you know about this Awardees?
Let us encourage you to provide any data which would enhance the completeness of this firm's profile.
Location Information
1331 Upland Building 2
Houston, TX 77043
Houston, TX 77043
(713) 463-6400 |
ebauer@actonmaterials.com |
www.actonmaterials.com |
Location: Single
Congr. District: 02
County: Harris
Congr. District: 02
County: Harris
Public Profile
Formerly known as ACTON Materials, Wells Signature Products LLC specializes in engineered powders and surfaces, which it produces in an advanced gas-solids reactor, the Mechanically Fluidized Vacuum (MFV) furnace. The firm has developed a new gas-solids reactor for simplified development of engineered powders and surfaces. The Mechanically Fluidized Vacuum (MFV) reactor is the first gas-solids furnace to simultaneously control all process parameters- including atmosphere pressure and composition, temperature, flow rate and reactant loading. Combining the most desirable features of vacuum furnaces and fluidized bed furnaces, ACTON's reactor supports the broadest range of deposition, diffusion and heat treatment capabilities ever found in a single piece of equipment. It is designed to complement or replace processes such as pack cementation, spray and fuse, gas fluidized bed treatment and physical vapor deposition (PVD). Benefits of the MFV system include Reducing the cost of several classes of coating, alloying and heat treating operations applied to both parts and powders o Ability to create novel, high-performance coatings, powders and alloys Engineered Powders: Since ACTON's reactor is much less sensitive to absolute particle size or particle size distribution than conventional systems, the size range capability extends from nano-scale to fractional inch powders. In almost all cases, the powder state can be maintained throughout processing, eliminating or minimizing the need for crushing, grinding and sizing. Processes supported include encapsulation, diffusion alloying, compounding (e.g., intermetallics), reduction/purification and vapor-phase synthesis of nano-scale powders. Powder lots from 25lb. to 1,000 lb. can be produced with currently-available equipment. The reactor is scalable for larger production requirements. Engineered Surfaces Surface modification can be accomplished by either of two methods: Direct surface conversion - deposition/diffusion of elements to form near-surface alloys or intermetallics. Applied coatings - thermal or electrolytic deposition of an engineered powder, sometimes followed by diffusion heat treatment. Novel bulk properties may be achievable using the ACTON reactor's unique capability to conduct a true vacuum quench. In the ACTON system, the quenchant can be a high-density, high melting point solid, eliminating vapor phases and attendant environmental problems.The Company ACTON is a materials technology company committed to reducing manufacturing cost across a broad range of powders and solid parts used in high performance applications. The company's core businesses are thermal spray powders, electro-magnetic powders and vapor-phase aluminizing of both parts and powders. Additionally, the company is conducting material development projects for clients in the automotive, tire, munitions and composite structures industries.
Extent of SBIR involvement
Synopsis: Awardee Business Condition
Employee Range
5-9Revenue Range
.5M-1MVC funded?
NoPublic/Private
Privately HeldStock Info
----IP Holdings
1-4Awards Distribution by Agency
Most Recent SBIR Projects
Year | Phase | Agency | Total Amount | |
---|---|---|---|---|
2005 | 2 | AF | $842,941 | |
Project Title: Waste Disposal/Waste Management System for Low Observable (LO) Composite Materials | ||||
2005 | 2 | AF | $302,095 | |
Project Title: Repair of High Temperature RAM Coatings |
Key People / Management
John E Kane -- President
Eric Bauer
Robert L Hance
Kim Wynns
Eric Bauer
Robert L Hance
Kim Wynns
Company News
There are no news available.