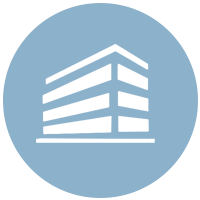
Busek Company Inc (AKA: Busek Co Inc) Profile last edited on: 2/6/2020
CAGE: 0T2F0
UEI: SATYSBWG3FL7
Business Identifier: Space propulsion, power electronics and controls, integrated space systems, and applied material science Is this YOUR Company?
Ensure accuracy and completeness of YOUR Company Profile by completing the brief Survey Instrument attached
Do you know about this Awardees?
Let us encourage you to provide any data which would enhance the completeness of this firm's profile.
Location Information
Location: Single
Congr. District: 05
County: Middlesex
Congr. District: 05
County: Middlesex
Public Profile
From its founding shortly after passage of the SBIR enablng legislation, Busek Co. Inc. became - and still remains - program involved. The firm is usefully understood as a spacecraft propulsion company providing thrusters, electronics, and complete systems for spacecraft. Busek spaceflight heritage includes the first US Hall thruster in space (TacSat-2),[2] the first electrospray thruster in space (LISA Pathfinder),[3] four micro-pulsed plasma thrusters flown aboard FalconSat-3,[4] and a BHT-200 Hall thruster flown aboard FalconSat-5.[5] Flight missions Busek products have spaceflight heritage on several missions, including: LISA Pathfinder The first spaceflight-qualified electrospray thruster was manufactured by Busek and launched aboard the European Space Agency's LISA Pathfinder satellite on December 3, 2015.[3] The micro-newton colloid-style electric thruster was developed under contract with NASAs Jet Propulsion Laboratory (NASA ST-7 Program), and part of NASAs Disturbance Reduction System (DRS) which serves a critical role in the LISA Pathfinder science mission.[8] TacSat-2 Busek's BHT-200 hall effect thruster The first US Hall thruster flown space, Busek's BHT-200, was launched aboard the Air Force Research Laboratorys (AFRL) TacSat-2 satellite.[9] The Busek thruster was part of the Microsatellite Propulsion Integration (MPI) Experiment and was integrated on TacSat-2 under the direction of the DoD Space Test Program. TacSat-2 launched on December 16, 2006 from the NASA Wallops Flight Facility.[2] FalconSat-3 Busek delivered four MPACS (Micro-Propulsion Attitude Control Systems) that launched aboard the Air Force Academys FalconSat-3 mission on March 8, 2007 from Cape Canaveral. The MPACS are integrated micro-pulsed plasma thrusters (microPPTs)[10] and the first US-designed and built coaxial microPPTs in orbit. MPACS provides precise attitude control on small (< 100 kg) satellites and are valuable for missions requiring precise pointing (e.g., high-resolution imaging).[4] FalconSat-5 Busek's Space Plasma Characterization Source was launched aboard the AFRL and USAF Academy's FalconSat- 5 satellite on November 2010.[11] The integrated unit consisted of an ammonia cold-gas thruster, a BHT-200 Hall effect thruster, high speed plasma probe, neutral source, propellant management system, Power Processing Unit (PPU), instrument electronics, and Digital Control Interface Unit (DCIU).[5] AEFH Aerojet, under license with Busek,[12][13] manufactured a 4 kW Hall thruster (the BPT-4000) which was flown aboard the USAF AEHF communications spacecraft. The thruster is credited with saving the first satellite by raising it to geosynchronous orbit after failure of the spacecraft's main apogee engine.[14] Research and development Propulsion Busek's BIT-3 ion thruster operating on several propellants Busek has demonstrated a variety of experimental xenon Hall thrusters at power levels up to and exceeding 20 kW.[15] Busek has also developed Hall thrusters that operate on iodine,[16][17] bismuth,[18][19] carbon dioxide,[20] and other substances. In 2008, a xenon fueled Busek Hall thruster appeared in National Geographic.[21] An iodine fueled 200 W Busek Hall thruster will fly on NASA's upcoming iSat (Iodine Satellite) mission. Busek is also preparing a 600 Watt iodine Hall thruster system for future Discovery Class missions. [22] Other publicized Busek technologies include RF ion engines[16][23] and a resistojet rocket.[24] Another focus is CubeSat propulsion,[16] proposed for the 2018 Lunar IceCube mission.[25] As of July 2012, Busek was also working on a DARPA-funded program called DARPA Phoenix, which aims to recycle some parts of on-orbit spacecraft.[26] In September 2013, NASA awarded an 18?month Phase I contract to Busek to develop an experimental concept called High Aspect Ratio Porous Surface (HARPS) microthruster system for use in tiny CubeSat spacecraft.[27][28] ORbital DEbris Remover (ORDER) In order to deal with human-caused space debris, Busek proposed in 2014 a remotely controlled vehicle to rendezvous with debris, capture it, and attach a smaller deorbit satellite to the debris, then drag the debris/smallsat-combination, by means of a tether, to the desired location. The larger sat would then tow the debris/smallsat combination to either deorbit or move it to a higher graveyard orbit by means of electric propulsion. The larger satellite is named the ORbital DEbris Remover, or ORDER which will carry over 40 SUL (Satellite on an Umbilical Line) deorbit sats plus sufficient propellant for the large number of orbital maneuvers required to effect a 40-satellite debris removal mission over many years. Busek is projecting the cost for such a space tug to be US$80 million.[29]is engaged in applied research, hardware development, and specialty manufacturing in two complementary lines of business: plasma applications and material science. The firm is a leading developer of advanced electric propulsion thrusters for use on military, government, and commercial satellites. In the materials processing area Busek offers bonding and brazing services for silicon carbide and other nonoxide ceramics. These processes allow the production of engineered parts from simple shapes, at low cost. Busek has developed bonding processes suitable for many of the major types of bulk and composite silicon carbide, Carborundum, Norton Saint Gobain, INEX, Morton International, Tenmat, Silicon Carbide Products, and Coors Ceramics. Busek's bonded and brazed products have been used to produce high temperature probes, heat exchangers and process tubes for industrial applications. Reaction Bonding 400X micrograph of silicon carbidejoint Tube to Plate bonds provide sealing surfaces The reaction joining process produces silicon carbide bonds between components. The parts are coated with a carbon-silicon spray on mating surfaces. The parts are assembled and heated to the melting point of silicon, 1400°C. The carbon and silicon between the parts react to form dense silicon carbide. Control over the composition, atmosphere, pressure, and the reaction-infiltration temperature allow production of high density, low residual silicon bonds
Extent of SBIR involvement
Synopsis: Awardee Business Condition
Employee Range
50-74Revenue Range
5M-7.5MVC funded?
NoPublic/Private
Privately HeldStock Info
----IP Holdings
15-19Awards Distribution by Agency
Most Recent SBIR Projects
Year | Phase | Agency | Total Amount | |
---|---|---|---|---|
2023 | 2 | NASA | $3,380,079 | |
Project Title: High Total Impulse BET-MAX System for Small-Sat Deorbiting | ||||
2023 | 1 | AF | $74,979 | |
Project Title: Flexible Fuel Electron Source for Space Propulsion Systems | ||||
2022 | 2 | AF | $749,996 | |
Project Title: Low Mass High Power Hall Effect Thruster for Enhanced Space Asset Resiliency | ||||
2022 | 1 | AF | $49,927 | |
Project Title: Low Mass High Power Hall Effect Thruster for Enhanced Space Asset Resiliency | ||||
2022 | 2 | AF | $899,976 | |
Project Title: High Density Plasma Thruster |
Key People / Management
Vlad J Hruby -- President and Founder
Akintunde I Akinwande
Saeed Anwar
Thomas R Brogan
Judy Budny
Lawrence T Byrne
Yu-Hui Chiu -- Director, Applied Sciences
Yu-Hui Chiu
Daniel Courtney
Craig Deluccia
Nathaniel Demmons -- Director
Eric Ehrbar -- Acting Director, Electronics
Manuel Gamero
Charles J Gasdaska
Samantha Gray
W Guss
David Hardy
Kurt Hohman -- Director, Electrothermal Thrusters
Thomas Jaquish
Xiaohu Liu
Manuel Martinez-Sanchez
Michael Mcguirk
Joshua Model -- Senior Electrical Engineer
J Monheiser
Lynn B Olson
Bruce Pote -- Director, Hall Thrusters
Lauren Rand
Lauren Rand-Lee
Thomas Roy
Douglas Spence -- Director of Flight Hardware and Micropropulsion
Douglas Spence -- Director, Flight Hardware Fabrication and Acting Director, Micropropulsion
James J Szabo
Zachary Taillefer
Rachel Tedrake
Michael Tsay
Luis Velasquez-Garcia
W Dan Williams -- Director Business Development
Jurg Zwahlen
Akintunde I Akinwande
Saeed Anwar
Thomas R Brogan
Judy Budny
Lawrence T Byrne
Yu-Hui Chiu -- Director, Applied Sciences
Yu-Hui Chiu
Daniel Courtney
Craig Deluccia
Nathaniel Demmons -- Director
Eric Ehrbar -- Acting Director, Electronics
Manuel Gamero
Charles J Gasdaska
Samantha Gray
W Guss
David Hardy
Kurt Hohman -- Director, Electrothermal Thrusters
Thomas Jaquish
Xiaohu Liu
Manuel Martinez-Sanchez
Michael Mcguirk
Joshua Model -- Senior Electrical Engineer
J Monheiser
Lynn B Olson
Bruce Pote -- Director, Hall Thrusters
Lauren Rand
Lauren Rand-Lee
Thomas Roy
Douglas Spence -- Director of Flight Hardware and Micropropulsion
Douglas Spence -- Director, Flight Hardware Fabrication and Acting Director, Micropropulsion
James J Szabo
Zachary Taillefer
Rachel Tedrake
Michael Tsay
Luis Velasquez-Garcia
W Dan Williams -- Director Business Development
Jurg Zwahlen